Control de Caldera para producción de vapor
- ingenieriadeproceo
- 4 mar 2021
- 6 Min. de lectura
Actualizado: 7 mar 2021
Calderas de vapor
Las calderas de vapor son calderas especialmente diseñadas para trabajar en instalaciones donde se necesite una gran transferencia de energía calorífica, como son procesos industriales (por ejemplo, la esterilización de las botellas antes del envasado), district-heating, lavanderías, hospitales, etc., así como para generar electricidad en centrales termoeléctricas.

A la caldera se le exige, pues, mantener una presión de trabajo constante para la gran diversidad de caudales de consumo en la factoría, por lo cual debe ser capaz de:
a) Aportar una energía calorífica suficiente en la combustión del fuel-oil o del gas con el aire.
b) Desde el punto de vista de seguridad, el nivel debe estar controlado y mantenido dentro de unos límites.
c) Es necesario garantizar una llama segura en la combustión.
d) El sistema de control debe ser seguro en la puesta en marcha, en la operación y en el paro de la caldera.
e) El funcionamiento de la caldera debe ser optimizado para lograr una rentabilidad y economía adecuadas, lo cual es posible con un control digital y/o distribuido que permite optimizar la combustión (ahorros del 2% al 10% en combustible) y ganar en seguridad.

Control de combustión
La regulación de la combustión se basa en mantener constante la presión de vapor en la caldera, tomándose sus variaciones como una medida de la diferencia entre el calor tomado de la caldera como vapor y el calor suministrado.
En la regulación de la combustión puede darse preferencia, en el mando, al combustible o al aire para que la operación de la caldera corresponda a un sistema determinado de variadas características de seguridad. Estas características de combustión son las siguientes:

Caudal fuel - caudal aire en serie
En el primer esquema de funcionamiento que puede verse en la figura 11.1a, el controlador de presión (master) ajusta el punto de consigna del controlador de caudal de fuel y esta variable actúa, a través del relé de relación fuel-aire, como punto de consigna del controlador de aire. Como las variaciones del caudal de fuel influyen lentamente en la señal de presión de vapor, el controlador "maestro" se ajusta para una respuesta rápida ante cambios en la presión. En esta disposición, si varía la presión del vapor, el caudal de fuel cambia antes que el del aire de combustión. Si se limita el caudal de fuel, lógicamente, también quedará limitado el caudal de aire.
La desventaja principal del sistema es el riesgo de explosión que se presenta ante un fallo de aire en el punto de consigna del controlador de caudal de aire; si así ocurre, no hay aire de combustión, pero el fuel continua circulando, acumulándose.
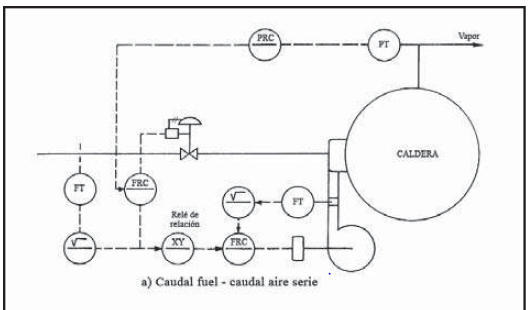
Caudal aire - caudal fuel en serie
Tal como puede verse en la figura 11.1b, aquí el controlador de presión (master) ajusta la señal de aire, el cual ajusta a través del relé de relación el controlador de fuel. El sistema es más seguro que el anterior ya que elimina la posibilidad de formación de una mezcla explosiva cuando falla la señal de aire de combustión.
Si la demanda de vapor disminuye, el fuel disminuye primero y luego lo hace el aire; y si la señal de aire falla, el caudal de fuel-oil baja a cero automáticamente.
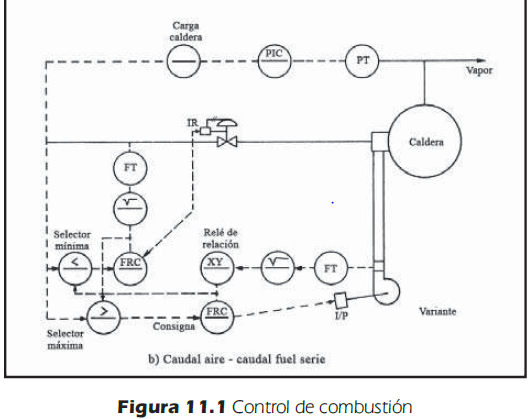
Presión de vapor - caudal fuel en serie/caudal vapor - caudal aire en serie
El sistema representado en la figura 11.1c se caracteriza por mantener, con más seguridad, la relación correcta aire-fuel aunque el fuel no sea medido correctamente. El controlador de presión de vapor ajusta el controlador de caudal de fuel. El transmisor de caudal de vapor ajusta el controlador de caudal de aire al sistema de control de combustión. Aunque las variaciones de caudal de vapor sean rápidas, las fluctuaciones que experimenta no lo son tanto como la presión de la línea de vapor principal. Este sistema se emplea con preferencia en calderas de carbón pulverizado.
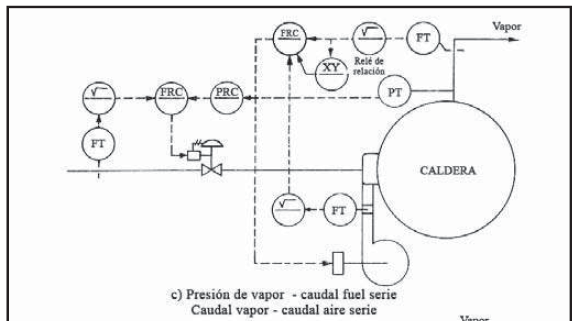
Caudal aire - caudal fuel en paralelo
La ventaja principal de este sistema, que puede verse en la figura 11.1d, es su control directo en el fuel y en el aire. De hecho, para mantener una relación correcta fuel-aire conviene incorporar un relé de relación manual al sistema. El sistema tiene un mayor rendimiento que el sistema en serie pero está limitado a calderas con pequeños cambios de carga.

Sistema cruzado de adelanto - retardo (lead-lag)
Es parecido al sistema paralelo pero incorpora un enclavamiento entre el fuel y el aire, de tal manera que el caudal de fuel sigue al caudal de aire si aumenta la carga y, si la carga disminuye, es el caudal de aire el que sigue al caudal de fuel. Tiene la ventaja de que previene la condición de peligro de exceso de fuel.
Este sistema se recomienda cuando los cambios de carga son oscilantes y dinámicos y permite un control preciso de la relación fuel/aire.

Control de la temperatura del Vapor
Existen calderas cuya producción es vapor saturado, de tal forma que la temperatura del vapor viene marcada por la presión de operación, pues son variables directamente relacionadas.
También existen calderas en las que el vapor es sobrecalentado de forma ligera para su mejor conducción o consumo, pero que se dimensionan de forma que las modificaciones en la temperatura del vapor no sean importantes de cara al consumidor. Sin embargo, hay gran cantidad de calderas en las que el vapor generado ha de estar a una cierta temperatura, que asegure el correcto funcionamiento de sus consumidores.
En estos casos, en los que normalmente el grado de sobrecalentamiento es mayor, la imposibilidad de diseñar la caldera para que en todas las cargas requeridas produzca el vapor a la temperatura deseada, obliga a controlar ésta de forma que se mantenga dentro de los márgenes de operación deseados.

En muchas calderas se utilizan recalentadores como medio para aumentar la temperatura del vapor por encima de la saturación (CALDERINES).
El atemperador inyecta agua en la línea de vapor, donde se vaporiza a su vez mezclándose con el vapor recalentado, produciendo el enfriamiento de este último.

Control de la Temperatura del Vapor.
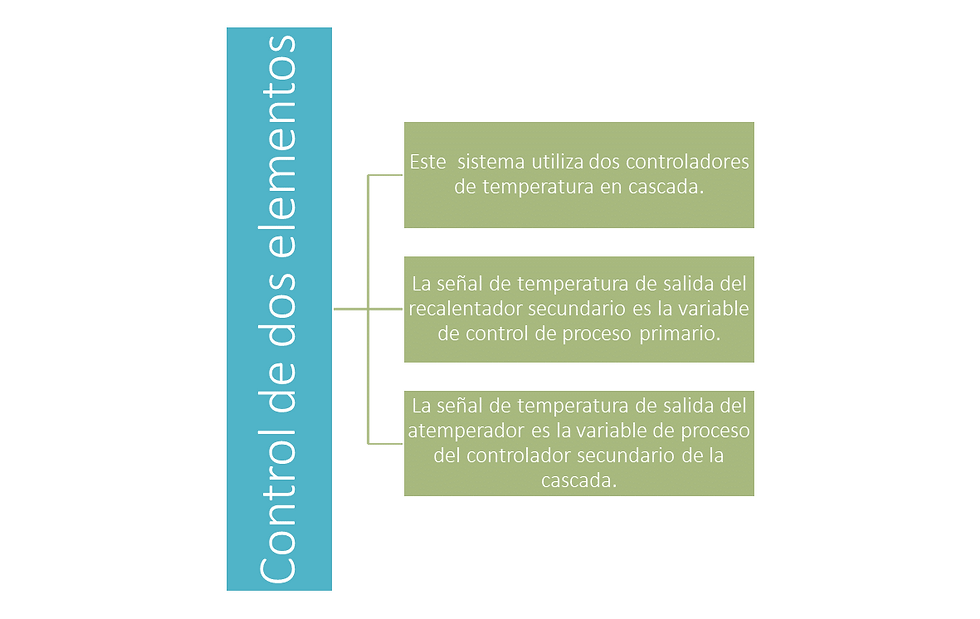
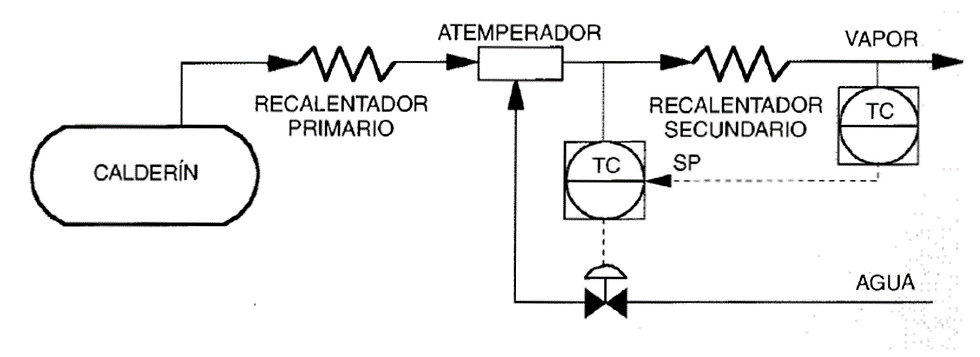
Control de Nivel
La regulación del agua de alimentación que establece el nivel de la caldera depende de múltiples factores, del tipo de caldera, de la carga, del tipo de bomba, y del control de presión del agua de la alimentación.


En calderas de pequeña capacidad, inferior a 1000 kg/h, la regulación puede ser todo-nada, con dos alarmas de nivel alto y bajo que ponen en marcha la bomba de alimentación del agua.

En calderas de capacidad media, (2000-4000 kg/h), puede utilizarse un controlador de flotador con un reóstato acoplado eléctricamente a una válvula motorizada eléctrica. Este conjunto actúa como un control proporcional con punto de consigna el punto medio del campo de medida del nivel de flotador.

En la regulación de nivel de un elemento, el único instrumento utilizado es el controlador de nivel que actúa sobre la válvula del agua de alimentación. El instrumento medidor de nivel puede ser del tipo desplazamiento o de presión diferencial de diafragma.

La regulación de nivel de dos elementos se logra con un controlador de caudal de vapor y un controlador de nivel, cuyas señales de salida se comparan en un relé de relación que actúa directamente sobre la válvula de control del agua de alimentación.
De acuerdo con la demanda de caudal de vapor, hay una aportación inmediata de agua de alimentación a través del controlador secundario de nivel. Este último sólo es utilizado como reajuste de las variaciones que pueden producirse con el tiempo en el nivel de caldera.
La regulación de tres elementos elimina el fenómeno de oscilación del nivel de agua que se produce cuando el caudal de vapor crece o disminuye rápidamente. Es un sistema recomendado en plantas con cargas dinámicas.
Cuando el caudal de vapor aumenta bruscamente, la presión baja, con lo que se produce una vaporización rápida que fuerza la producción de burbujas y agua, lo que da lugar al aumento aparente del nivel de la caldera. La oscilación es opuesta a la demanda y el fenómeno es importante en calderas de cierta potencia y volumen reducido, sujetas a variaciones de caudal frecuentes y rápidas.
Las tres variables que intervienen en el sistema son:

Para que las condiciones de funcionamiento sean estables, el caudal de vapor y el de agua deben ser iguales y, de forma secundaria, el nivel de agua debe reajustarse periódicamente para que se mantenga dentro de unos límites determinados (normalmente son de unos 50 mm por encima y por debajo de la línea central de la caldera).
Manteniendo estas funciones en las tres variables, los instrumentos correspondientes pueden estar relacionados entre sí de varias formas. Las más representativas se muestran en la figura, en las que una señal anticipativa (feedforward) del caudal de vapor se superpone al control de nivel, y todas tienen por objeto dar prioridad a las diferencias entre los caudales de agua y de vapor frente a las variaciones del nivel que pueden producirse ante una demanda súbita, es decir, en estas condiciones el sistema de control actúa obedeciendo a la diferencia relativa de caudales con preferencia a los cambios en el nivel.

Es bueno señalar que la medida del caudal de vapor se efectúa preferentemente con una tobera porque su forma suave evita la erosión que, de otra forma, se produciría en una placa-orificio por causa de las gotas de agua que inevitablemente arrastra el vapor. El caudal de agua de alimentación puede medirse a través de una placa-orificio o de una tobera.
Hemos elaborado un vídeo explicativo en donde podrás conocer un poco más de esta temática: https://youtu.be/VeBvAiq6LPw
Bibliografía
Creus, A. (2010). Instrumentación Industrial. Mexico: Alfaomega grupo Editor, S.A de C.V .
Sanchez, J. (2002). Control avanzado de Proceso. Madrid: Ediciones Díaz De Santos S.A.
Comments