TRANSMISORES
- ingenieriadeproceo
- 23 ene 2021
- 9 Min. de lectura
Actualizado: 4 mar 2021
INTRODUCCION
En cualquier proceso es absolutamente necesario controlar y mantener constantes determinadas medidas, como presión, caudal, nivel, temperatura, pH, conductividad, velocidad, humedad, punto de rocío, etc. Los instrumentos de medida y control pueden mantener y ajustar estas constantes en condiciones más adecuadas que las que puede realizar el propio operador.
Definición
El transmisor es un instrumento que capta la variable en proceso y la transmite a distancia a un instrumento indicador, registrador, controlador o una combinación de estos.
Los transmisores, también denominados transductores, sirven para convertir las magnitudes físicas clásicas en una señal eléctrica.
Para poder comparar y procesar distintas magnitudes físicas, es necesario recurrir a los transmisores.
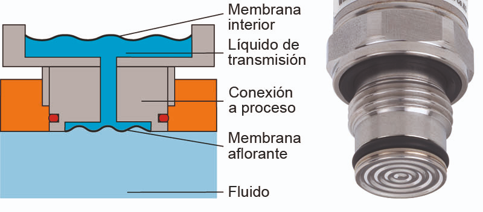

PRINCIPIO Y FUNCIONAMIENTO
La función primordial de este dispositivo es tomar cualquier señal para convertirla en una señal estándar adecuada para el instrumento receptor, es así como un transmisor capta señales tanto de un sensor como de un transductor, aclarando siempre que todo transmisor es transductor más no un transductor puede ser un transmisor; •como ya se conoce, las señales estándar pueden ser neumáticas cuyos valores están entre 3 y 15 Psi, las electrónicas que son de 4 a 20 mA o de 0 a 5 voltios, las digitales que entregan 0 o 5 voltios para 0 o 1 respectivamente.
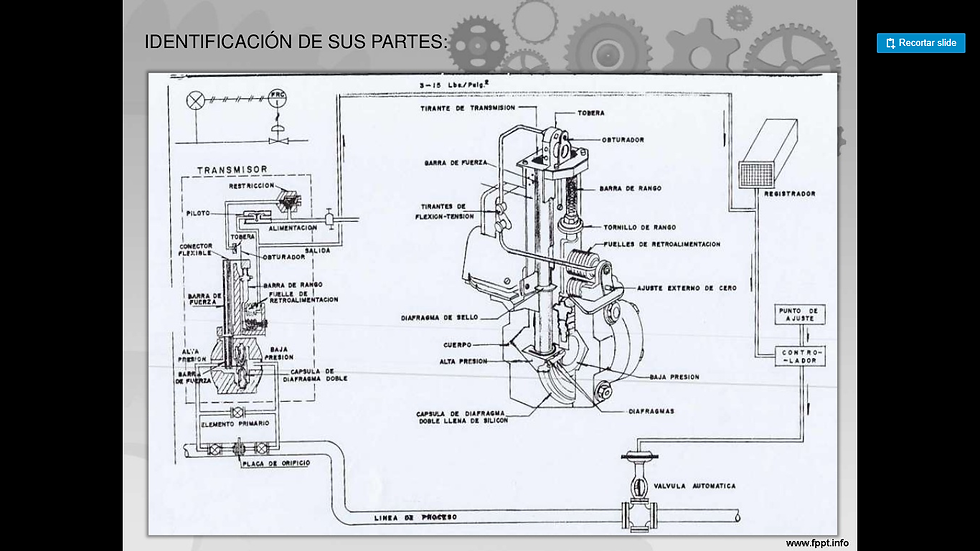
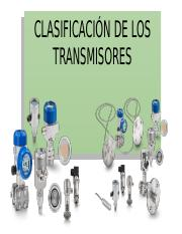

Transmisores neumáticos
Los transmisores neumáticos se basan en el sistema tobera-obturador que, mediante bloques amplificadores con retroalimentación por equilibrio de movimientos o de fuerzas, convierte el movimiento del elemento primario de medición a una señal neumática de 3-15 psi (libras por pulgada cuadrada) o bien su equivalente en unidades métricas 0,2-1 bar (0,2-1 Kg/cm2) (20-100 kPa), siendo su exactitud del orden del ± 0,5%.
Este sistema es básicamente un tubo neumático que se alimenta a una presión constante Pk y el cual tiene una restricción en su salida en forma de cañón o tobera el cual puede ser obstruida por una laminita que comúnmente se le conoce como: OBTURADOR y ésta básicamente depende de una posición que está interconectada en función del elemento de medida. A continuación, presentamos el gráfico que describe perfectamente este sistema.

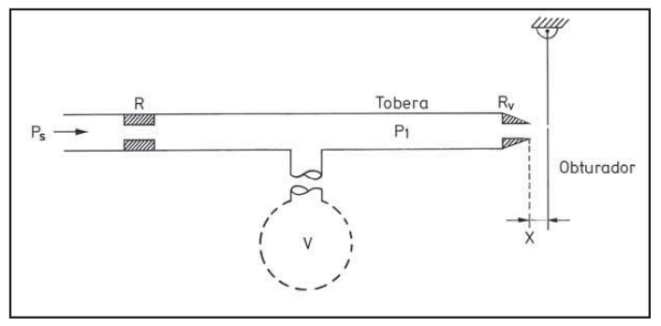
El aire que alimenta el sistema debe estar normalizado aproximadamente a 1,4 bar equivalente a 20 psi, este debe pasar por la restricción R y llenar el volumen que se encuentra cerrado y está denotado por V para que de esta forma se escape por la tobera Rv. Esta posee un diámetro muy pequeño que ronda los 0,25 a 0,5 mm, mientras que la restricción R posee un diámetro que ronda los 0.1mm. Con el obturador abierto la presión que entra posteriormente es de alrededor 0,03 bares. Esto indica que la relación de presiones diferenciales en conjunto con la restricción R es de 1,4/0,03 aproximadamente 50 veces. El consumo de aire entre el sistema tobera-obturador, es relativamente pequeño, del orden de 3 N1/min.
A continuación, se puede apreciar una curva de respuesta típica de un sistema tobera-obturador donde podemos apreciar que la misma no es lineal. Lógicamente el comportamiento de este sistema es no-lineal.
El aire que se escapa de la tobera ejerce una fuerza sobre el obturador cuya relación es: F= P1 X S que tiende a desplazarlo. Esta fuerza debe hacerse despreciable con relación a la fuerza del elemento de medida que posiciona el obturador.
Con este objeto, en el circuito acondicionador conformado por un amplificador de dos etapas se utiliza solo una pequeña parte reducida de la curva y se disminuye además la sección de la tobera a diámetros muy pero muy pequeños de 0,1 a 0,2 mm los cuales no son considerados diámetros más pequeños para evitar que la respectiva tobera se tape por suciedad de aire. De este modo se logrará una relación prácticamente lineal entre en valor de la variable y la señal que es transmitida.

Transmisores electrónicos
Basados en detectores de inductancia, o utilizando transformadores diferenciales o circuitos de puente de Wheatstone, o empleando una barra de equilibrio de fuerzas, convierten la señal de la variable a una señal electrónica de 4-20 mA c.c. Su exactitud es del orden del ± 0,5%.
Para cada valor de la presión, la barra adopta una posición determinada excitándose un transductor de desplazamiento tal como un detector de inductancia, un transformador diferencial o bien detector fotoeléctrico. Un circuito oscilador asociado con cualquiera de estos detectores alimentan una unidad magnética y la fuerza generada reposiciona la barra de equilibrio de fuerzas. Se completa así con un circuito de realimentación variando la corriente de salida en forma proporcional al intervalo de presiones del proceso.
En el transmisor de equilibrio de fuerza con detector fotoeléctrico, la barra rígida tiene en un extremo una ventanilla ranurada que interrumpe total o parcialmente un rayo de luz que incide en una cédula fotoeléctrica de dos elementos.
Análogamente a los instrumentos neumáticos, no pueden guardar las señales de planta, y además son sensibles a vibraciones, por cuyo motivo su empleo ha ido disminuyendo.
El transmisor electrónico se alimenta con una fuente de 24 V c.c. y un circuito de dos hilos. El receptor dispone de una resistencia de 250 ohms conectada en los bornes de entrada. De este modo, si la señal de salida del transmisor varía de 4 mA c.c. a 20 mA c.c., se obtendrán las siguientes tensiones en los bornes de entrada al receptor:
250 ohmios × 4 mA c.c. = 1.000 mV = 1 V
250 ohmios × 20 mA c.c. = 5.000 mV = 5 V

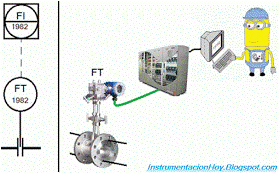
Es decir, de 1 V c.c. a 5 V c.c. y no se pierde tensión en la línea ya que la resistencia de 250 ohms está conectada justo a la entrada del receptor.
Transmisores digitales
Cuando apareció la señal digital aplicable a los transmisores, mejoró notablemente la exactitud conseguida en la medida. La señal del proceso es muestreada a una frecuencia mayor que el doble del de la señal (teorema de muestreo de Nyquist-Shannon) y de este modo, la señal digital obtenida consiste en una serie de impulsos en forma de bits.
Cada bit consiste en dos signos, el 0 y el 1 (código binario), y representa el paso (1) o no (0) de una señal a través de un conductor. Si la señal digital que maneja el microprocesador del transmisor es de 8 bits entonces puede enviar 8 señales binarias (0 y 1) simultáneamente. Como el mayor número binario de 8 cifras es:
11111111 = 1 + 1×2^1 + 1×2^2 + 1×2^3 + ... + 1×2^7 = 255
se sigue que la exactitud obtenida con el transmisor debida exclusivamente a la señal digital es de:
(1/255) × 100 = ± 0,4%
El término "inteligente" (smart) indica que el instrumento es capaz de realizar funciones adicionales a la de la simple transmisión de la señal del proceso. Estas funciones adicionales pueden ser:
· Generación de señales digitales.
· Comunicabilidad.
· Uso de otros sensores tales como de presión y temperatura para compensar las variaciones del fluido y conseguir una mayor exactitud.
· Cambio fácil de rangos. La "inteligencia" se aplica también a otras variables, tal como la temperatura donde el transmisor puede trabajar con distintas sondas de resistencia y termopares y diversos campos de medida, gracias a la linealización de las escalas y a la compensación de la unión fría que aporta el microprocesador.
Hay dos modelos básicos de transmisores digitales inteligentes, el capacitivo y el de silicio difundido.
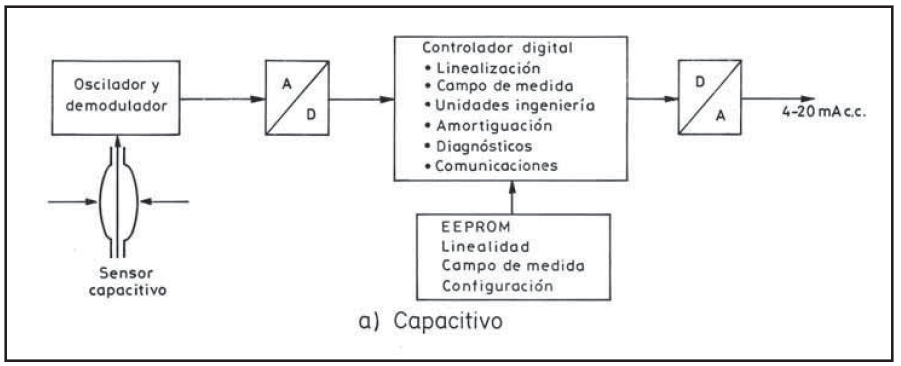

Transmisor inteligente capacitivo
El sensor capacitivo está basado en la variación de capacidad que se produce, en un condensador formado por dos placas fijas y un diafragma sensible interno y unido a las mismas, cuando se les aplica una presión o presión diferencial a través de dos diafragmas externos. La transmisión de la presión del proceso se realiza a través de un fluido (aceite) que rellena el interior del condensador.
El desplazamiento del diafragma sensible es de sólo 0,1 mm como máximo. Un circuito formado por un oscilador y demodulador transforma la variación de capacidad en señal analógica. Ésta, a su vez, es convertida a digital y pasa después a un microprocesador "inteligente" que la transforma a la señal analógica de 4-20 mA c.c y alimenta las comunicaciones digitales.
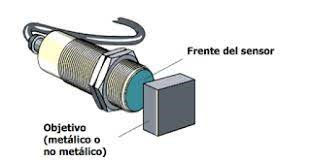
Transmisor inteligente piezoresistivo.
El sensor piezoresistivo está fabricado a partir de una delgada película de silicio y utiliza técnicas de dopaje para generar una zona sensible a los esfuerzos. Se comporta como un circuito dinámico de puente de Wheastone que incorpora un microprocesador.
Cuando no hay presión, las tensiones E1 y E2 son iguales y, al aplicar la presión del proceso, RB y RC disminuyen su resistencia y RA y RD la aumentan, dando lugar a caídas de tensión distintas y a una diferencia entre E1 y E2. Esta diferencia se aplica a un amplificador de alta ganancia que controla un regulador de corriente variable. Un margen de corriente continua de 3 a 19 mA con 1 mA del puente produce una señal de salida de 4 a 20 mA c.c. Esta corriente circula a través de la resistencia de realimentación RFB y eleva E1 a una tensión equivalente a E2 y reequilibra el puente. Como la caída de tensión producida a través de RFB es proporcional a RB, esta resistencia fija el intervalo de medida (span) del transductor. El cero del instrumento se varía intercalando resistencias fijas en el brazo izquierdo del puente (cero basto) y un potenciómetro en el brazo derecho (cero fino).


El elemento de medida incorpora tres sensores: presión diferencial, temperatura y presión estática. El cuerpo del medidor y la caja electrónica son muy robustos y resisten vibraciones, corrosión y humedad.
Ventajas e inconvenientes
En los instrumentos inteligentes, de salida electrónica o digital, en par_ cular en los transmisores, la calibración se ve facilitada por la "inteligencia" proporcionada por el microprocesador incorporado en el instrumento, alcanzan exactitud de ± 0,1%.
Ventajas
Cambio automático del campo de medida, caso de que el valor de la variable salga del campo y fijación de la variable en el último valor alcanzado, caso de detectarse alguna irregularidad en el funcionamiento del aparato.
Compensación de las variaciones de, temperaturas con autoajustes desde el panel de control.
Mantenimiento. Así pues, tanto en la puesta en marcha como en operación, los instrumentos "inteligentes" no precisan de aparatos patrón para su calibración, pues disponen de datos almacenados en EEPROM en fábrica (bajo normas NBS), por lo que la eventual calibración que pueda realizarse en el taller será de peor calidad que la efectuada con el comunicador
Rangeability, (relación señal máxima/señal mínima o dinámica de medida).
Auto-calibración por variaciones del proceso. Los transmisores inteligentes también disponen de auto calibración, es decir, suplen las operaciones del ajuste del cero y del 100 de los instrumentos, trabajo desarrollado clásicamente por los instrumentistas.
Autodiagnóstico. Proporcionan información de manera automática para que el departamento de mantenimiento tome lasas acciones correctivas.
Comunicador portátil. Para visualizar la señal de salida, los datos de configuración, el margen de funcionamiento y otros parámetros, y cambiar los ajustes del campo de medida se utiliza un comunicador portátil, que se conecta en cualquier punto de la línea de transmisión.
Ordenador personal (PC). El transmisor, o varios transmisores, pueden conectarse, a través de una conexión RS-232, a un ordenador personal que con el software adecuado es capaz de configurar transmisores inteligentes.
Desventajas.
· Normalización de las comunicaciones digitales, no está plenamente resuelta.
· Respuesta frecuencial defectuosa. Dependiendo de la frecuencia de la señal, ésta será transmitida da con poca fidelidad por el retardo inherente del microprocesador que debe realizar secuencialmente diferentes acciones de cálculo.
Ventajas e Inconvenientes de los Transmisores Digitales
En los instrumentos inteligentes, de salida electrónica o digital, en par cular en los transmisores, la calibración se ve facilitada por la "inteligencia" proporcionada por el microprocesador incorporado en el instrumento. Este guarda digitalmente en una EPROM los datos que proporcionan correcciones precisas de las no linealidades de los sensores ante las variaciones en la temperatura y en la presión ambiente.
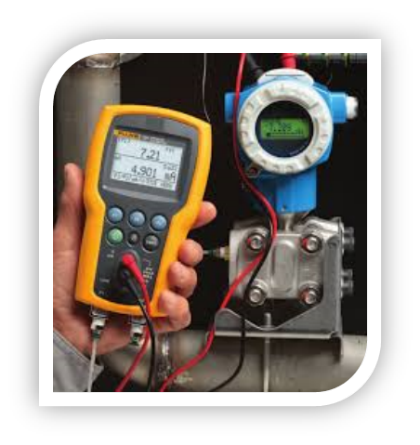

Aplicación en la Industria
Los transmisores son apropiados para numerosas tareas de medición industriales en distintas aplicaciones. Permite realizar una lectura del valor de medición in situ y transmitirlo a un sistema de control del proceso o un puesto de mando. Supervisan bombas, registran niveles de llenado en recipientes o realizan mediciones de caudal en tuberías.
Por lo general, tienen aplicaciones en la industria de procesos, maquinaria e instalaciones industriales, sector farmacéutico, la petroquímica e industria alimentaria, principalmente en la fabricación de bebidas.
Las aplicaciones dependerán de la necesidad y las variables a medir en el proceso, así como también del ambiente al que va a ser expuesto el instrumento.
Por ello es bueno conocer las ventajas y desventajas de los diferentes transmisores.

Una de las aplicaciones en la industria consultada en documentos electrónicos fue una propuesta de instalación de un transmisor de nivel por presión diferencial usado para la detección de interface en tanques de Petróleo.
El transmisor medirá el nivel, que será usada como entrada para un Controlador Lógico Programable, el cual comandará la abertura y cierre de las válvulas de salida de aceite en los tanques con la intención de garantizar la máxima salida de agua en el fondo del tanque sin presencia de aceite.

Sí deseas conocer más de esta propuesta puedes dar clic en el siguiente link:
Así también existe un estudio sobre la instalación de transmisores de presión y análisis de todos los componentes que componen el equipo de esterilización del sistema UHT (Temperatura Ultra Rápida), este transmisor tiene como finalidad hacer el monitoreo de presión del producto que tiene que ser mayor que la presión del agua en el intercambiador de calor tubular. Cuando la presión del producto sea menor que la requerida para el funcionamiento normal del sistema (0,3 bar), ocurrirá una falla en el mismo ocasionando la parada total de la planta.
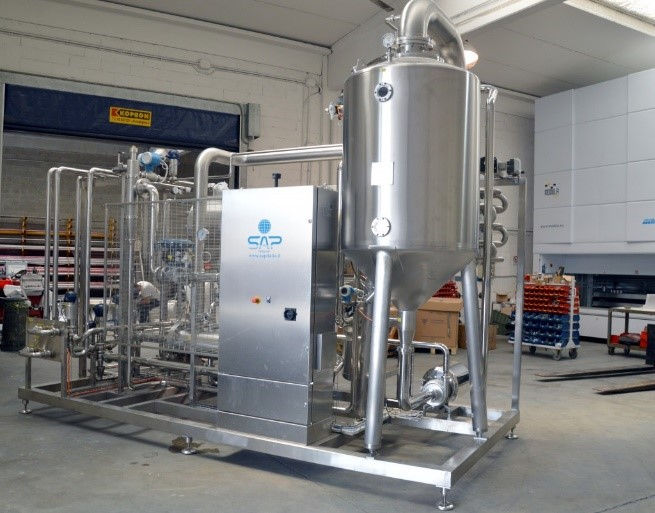
Este es el link de esta investigación, esperamos que te sirva:
Video de la exposición
Comments